In the field of Maintenance and Reliability (M&R), there is a key distinction that is often overlooked: results are not managed, they are produced. The key to achieving those results lies in managing the behaviors that generate them. This is something a manager I once had constantly emphasized (Thank you, Solange Pérez M. ). This approach is not only subtle in its definition but has a profound impact on the final outcomes of any organization.
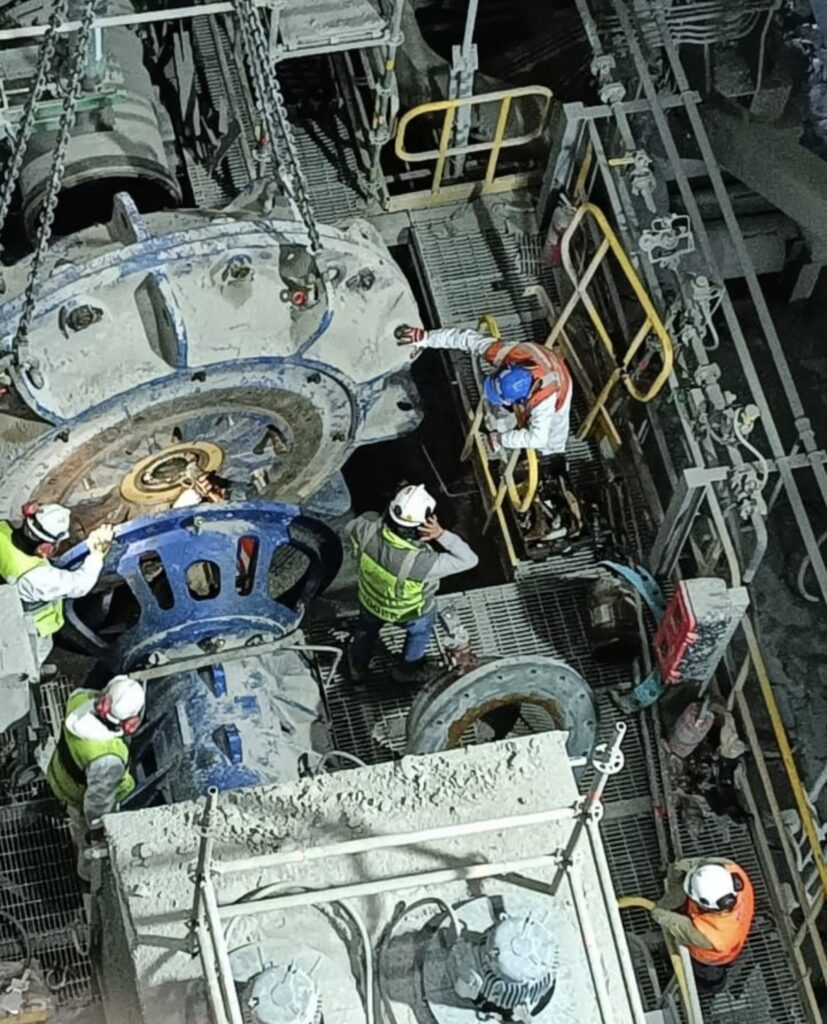
To achieve continuous improvement in Maintenance and Reliability, it is essential to manage the behaviors that produce the desired results.
Results vs. Behaviors
Results are the final product of a series of specific behaviors. No result ever occurs without a behavior that causes it, allows it, or influences its direction. Therefore, to improve results, we must focus on managing behaviors under certain circumstances and then measure the results.
For example, rather than focusing solely on final results like availability or maintenance costs, it is crucial to focus on the actions that generate them, such as compliance with preventive maintenance programs or the ratio of planned work versus reactive work. How often do we break the weekly plan? Or what is causing a backlog in planning?
Behavioral Metrics and Results Metrics
Instead of using terms like lagging and leading metrics, which may suggest a lack of control over the results, it is more useful to talk about Behavioral Metrics and Results Metrics:
- Behavioral Metrics: These measure the decisions and actions taken by teams, such as maintenance schedule compliance, percentage of proactive work, or the amount of planned work. These metrics are key indicators that allow day-to-day management of maintenance and help prevent undesired outcomes.
- Results Metrics: These evaluate the effects or outcomes produced, such as equipment availability, maintenance costs, MTBF (Mean Time Between Failures), or MTTR (Mean Time to Repair). These metrics directly reflect the impact that behaviors have had on the system.
Many organizations make the mistake of focusing exclusively on Results Metrics without understanding which behaviors are driving those numbers. To me, this is like gambling in a casino. This lack of connection can lead to changes based on guesswork, which puts continuous improvement at risk.
The Importance of Coaching
Another fundamental aspect of Maintenance and Reliability is the ongoing training of technicians, especially in Predictive Maintenance (PdM) technologies. Experience has shown that personalized coaching in the technician’s work environment, using their equipment and daily-use software, is much more effective than sending staff to formal classes. Once again, this coaching must be measurable to track progress and reinforce weaknesses.
One-on-one coaching allows for individualized attention, where specific questions can be addressed, and the teaching can be adjusted to the technician’s needs and skills. This is particularly valuable in specialized areas, which can be broken down into several categories, each requiring a different approach to achieve high performance:
1. Knowledge of Industry Standards and Best Practices
It is essential for maintenance leaders to be familiar with international standards (such as ISO 55000 for asset management) and best practices within the industry. This knowledge ensures that maintenance operations are carried out efficiently and in compliance with standards that promote reliability, safety, and sustainability of assets.
2. Strategic Maintenance Planning
The ability to strategically plan maintenance is crucial for maximizing equipment lifespan and minimizing downtime. This involves a proactive approach that combines preventive, predictive, and corrective maintenance, based on equipment criticality and its impact on production. Effective planning reduces unplanned interventions and optimizes resource usage.
3. Integration of Predictive Maintenance Technologies
Instead of relying solely on reactive maintenance, companies must leverage predictive maintenance technologies, such as vibration analysis, thermography, ultrasound, and oil analysis. Integrating these tools allows for a holistic view of equipment health, enabling better decision-making on when to intervene before a failure occurs.
4. Optimization of Spare Parts and Resource Management
Efficient management of spare parts and resources is fundamental to avoiding delays in maintenance. This involves maintaining an optimized inventory of critical components and ensuring that personnel have access to the right tools and equipment when needed. Effective spare parts management prevents extended equipment downtime due to a lack of parts.
5. Continuous Monitoring and Data Management
Modern industries demand continuous monitoring of asset conditions in real-time to identify problems before they cause disruptions. Adopting condition monitoring systems helps detect trends and anomalies, while effective data management ensures that the collected information is used for predictive analysis and data-driven decision-making, not just guesswork.
6. Development of Multidisciplinary Skills in Personnel
Maintenance teams can no longer operate in isolated silos. It is important for technicians to develop skills in various areas of maintenance, from predictive technologies to automation and control systems. This multidisciplinary approach provides greater operational flexibility and ensures that maintenance teams can tackle a wide range of challenges without excessive reliance on external personnel or specialists.
7. Lifecycle Cost Management of Assets
Managing the lifecycle cost (LCC) of assets is a critical aspect of modern maintenance. It’s not just about repairing or replacing equipment, but understanding the total cost of ownership over its entire lifespan. This includes acquisition, operation, maintenance, and eventual disposal costs. Maintenance leaders should focus on minimizing these costs while maximizing efficiency and reliability.
8. Risk-Based Decision Making
In an industrial environment with limited resources, risk-based decision making is key. Maintenance leaders must be able to evaluate the risks associated with equipment failure and prioritize their actions accordingly. Decisions informed by asset criticality and the impact on production or safety ensure that resources are allocated where they are needed most.
Each technician has strengths and weaknesses in these areas, and a good coach can identify where more help is needed, leading to significant progress and preventing the formation of bad habits, poor practices, or misconceptions.
Importance Based on Real Industry Needs:
The evolution of the industry demands that maintenance is not just about fixing failures but preventing them and managing assets efficiently to maximize their value. Today’s competition revolves around availability, reliability, and cost optimization. To achieve this, organizations must combine technology with strategy. It’s essential to have real-time monitoring systems and predictive tools, but also effective planning and asset management that considers the entire lifecycle.
Additionally, continuous training and development of personnel and their ability to integrate advanced technologies is a constant need. Companies that do not invest in their technical teams risk losing their competitive edge. Moreover, the integration of digital systems and the use of real-time data analytics are already a standard in Industry 4.0.
In summary, success in modern maintenance depends on a comprehensive approach that considers both technology and the effective management of human and material resources. Companies that master these aspects will be able to reduce costs, increase reliability, and improve profitability in an increasingly competitive industrial environment.
OK Ok Ok, so in Conclusion
Once again, in just in case you forget or in case I wasn’t clear, to achieve continuous improvement in Maintenance and Reliability, it is essential to manage the behaviors that produce the desired results. Additionally, investing in personalized coaching can accelerate the development of technicians’ skills, thereby improving overall performance. By combining clear behavioral metrics with results metrics, organizations can make informed decisions and avoid falling into the cycle of arbitrary changes that fail to address the true causes of problems.
And as James Neale say, the key question for any leader in this field is: Are you measuring and managing the right behaviors to produce the results you’re aiming for?